Cement-sand mortar: the pros and cons
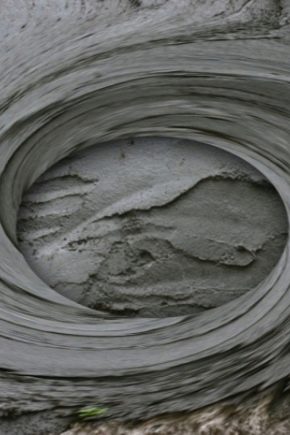
Virtually no repairs can do without the use of cement-sand mortar. There are many options for how and where it can be applied, but for proper use you need to know about all the advantages and disadvantages of this substance.
The quality of the material, the correct ratio of its parts will make it possible to make a good repair, which will last a long time.
Special features
Solutions used in construction can be of two types - cement or concrete. Concrete is characterized by the presence of crushed stone or gravel. The cement mortar contains three components: cement, sand and water. The quality of each product must be of the highest. For cement, the absence of moisture in the composition and the presence of lumps is important. The best option of sand - river, but you can take and ordinary, and the water should be clean and without impurities.
To the solution quickly and properly hardened, the water temperature must be at least twenty degrees.
Cement-sand mortar is needed for laying bricks and plastering. It is convenient to work with such a mixture, although a significant disadvantage is its relative hardness and rapid solidification, which forces one to fit in an hour and a half to use the mixed solution.
To solve this kind of problem, professionals use various additives that can significantly extend the life of the substance, making it as flexible as possible.
Cement-sand mortar is also used to seal cracks in walls and ceilings. The mixture is firmly held in place, not allowing the product to continue destruction. Besides, with the help of cement composition, you can pour a high-quality and reliable floorwhich will serve many years and will be convenient in operation.
The advantage of such a material can be considered resistance to moisture, temperatures and even sunlight. It is easy to work with cement, because it adheres well to almost all materials - both brick, and cinder block and stone will firmly hold on to the solution with cement.
Among the shortcomings, we can note a rough layer of the finished material, for which additional use of the finishing layer of plaster is necessary if the surface is painted or covered with wallpaper. Working with such a solution it is important to understand that it has a considerable weight, which means that a large amount of the substance laid on the wall will bear an additional load on the foundation.. If it is necessary to lay the solution on a painted or wooden surface, then adhesion with them will be minimal.
It would be undesirable to apply cement over the gypsum surface., because the weight of the solution is more, which will lead to tearing off part of the gypsum structure.
Apply the cement-sand mortar should be carefully. The minimum layer thickness is 5 mm, and the maximum thickness is 3 cm. A thinner layer will spread, and for a thicker coating, a reinforcing mesh is used and the work is done in stages, waiting for the complete drying of each layer.
The popularity of cement-sand mortar consists in the fact that for its preparation it is not necessary to use any special devices, anyone can make a batch, the main thing is to make the components correctly.Affordable price makes this mixture relevant for many years.
Specifications
For a good quality cement-sand mortar it is necessary to know all the technical characteristics of this composition, what is the GOST for each element, a specific type of work and how much material is needed to work on m³.
Characteristics of the substance can be considered on the basis of indicators:
- Densitywhat depends on the strength of the finished material and thermal conductivity. If the solution is used in its pure form without impurities, then this is a heavy material, the density of solidification of which is 1600-1800 kg per m³. This material will be enough for high-quality finish, both inside and outside the room. You can use it for floor screed.
- Thermal conductivity, which has high rates due to the high density of the solution. If we compare such a solution with gypsum, which has good thermal conductivity and stores heat for a long time, having a coefficient of 0.3 W, then the cement-sand mortar has an indicator of 0.9 W.
- Vapor permeabilitywhich is important for arranging walls that have the ability to remove excess heat to the outside so that condensate does not accumulate and humidity in the room does not form.Gypsum with cement have approximately equal indicators in this aspect, which are 0.11-1.14 for gypsum and 0.9 mg / mchPa for mortar with cement.
- Drying timewhich should be from 12 to 14 hours for a layer of two centimeters at an ambient temperature of 15 to 25 degrees. With an increase in the thickness of the cement, the time for how quickly the composition will become dry will increase. For optimal results, it is better to leave the product alone for at least one day.
- Weight, which can determine the mass acting on the product. It is difficult to accurately calculate the weight of the solution, because it depends on the components it contains, so the sand itself can be different, which also changes the final indicator. Standard sand of 1 mm will weigh 1,400 kg per m³, and if the grain has a size of 1.5 mm, the weight will increase to 1,700 kg, because, based on SNiP data, the weight of the cement-sand mortar is equal to 1,800 kg per m³.
Knowing all the indicators of the solution, you can properly mix its parts and get a qualitative composition for work.
Kinds
Cement mortars may have differences in the components, and therefore vary, which leads to different types of the given building material.
Among them:
- Normal solution - it should be the optimal amount of aggregate and binder. Kneading it with a paddle, you can notice sticking individual bunches on it.
- Fattyin which the amount of binder exceeds the aggregate. This leads to cracking of the solution after it has completely solidified. Understand that the solution turned out to be bold, if it will envelop the tool for kneading.
- Skinnyin which the amount of aggregate exceeds the binder. This makes the ready solution too liquid, it is extremely inconvenient to work with it. At the oar he does not stick, but only smears it.
Only by preparing the solution correctly, you can get the optimum consistency, which will be convenient to use, and the result will please with its quality. Perlite sand can be used in the process of preparation of the mixture, where the clay will be the main component, which will allow you to make not a cement, but a clay solution.
The use of this composition allows the surface to obtain a large thermal conductivity.
In addition to the cooking process itself it is important to know which brand of cement to use. Decoding the values on the package allows you to quickly and correctly select the necessary materials for a particular type of work.
There is a large variety of solutions - M10, 25, 50, 75, 100, 125, 150, 200, 250 and 300. For construction work the most commonly used brands are M75 and M150.
Mason mortar M100 requires the presence of cement M400 and sand, which are mixed in a ratio of 1: 4. The mixture obtained is best suited for working with a limestone and a cinder block. For the M200 solution it is necessary to take 1 part of M400 cement and two parts of sand. The finishing mortar is made of cement M400 or M500 and sand with water, which are correlated in proportions: 1: 3: 0.5. Also for the decoration of walls, you can take cement, sand and lime milk in a ratio of 1: 5: 2. Using a non-shrinking solution, it will be possible to qualitatively seal all cracks in the surface.
Conducting the kneading of any variant of the cement mass, it is important to understand when the optimal composition is obtained.
The finished solution will be held on the surface, which is turned over, when applying cement with a thickness of three millimeters. If it falls, then the bulk of the cement is above the norm and the composition is heavy, it is worth adding a little sand.
Application area
It is possible to use cement-sand mortar for various works, among which are:
- facade decoration;
- plastering and leveling of various surfaces for rooms without heating and those in which the humidity level is significantly increased;
- seal joints and cracks inside and outside the room;
- alignment of surfaces in which there are major defects, irregularities and potholes;
- the process of preparing the walls on which to lay tiles.
If you have to work with stone or wood, it is better to choose a cement-lime mortar. For the correct use of the mixture, it is necessary to clearly understand what is to be done, because for each type of work there is a different solution.
Masonry type is needed in order to fill the foundation and to put the pillars and arches. He holds well and aerated. To prepare such a solution can be with the use of impurities and without them. If the work will not last long, it is better not to add anything to the composition, and in the case of prolonged labor it is better to stimulate the plasticity of the composition and extend its capacity.
Mounting type is used to fill seams in blocks and panels of ready-made structures.. To make such a solution is not difficult, the main thing is to correctly calculate the quantity so that it does not freeze before the work is completed.It is better to knead a small amount and make a new composition upon completion of the old one, than to fill the gaps with a hard and non-ductile material.
Plaster type is needed to finish the walls and ceiling inside and outside the room. Mixing such a solution will have quite a lot, because the area for the application has considerable dimensions, and the speed of work will not allow the composition to harden.
If necessary, you can dissolve it a little, using the necessary additives, which will extend the life of the mortar.
Narrow-directional type is used for room decoration, waterproofing, plugging and similar purpose in the room.. Choosing the right brand, using the right proportions will allow you to get the right option, which you can perform the necessary construction activities.
Cooking
If home repair involves the use of a small part of the cement mortar, then it is better to buy a ready-made version, which will speed up the process itself, but in the case of a large scale of work, it will be cheaper and more economical to buy the necessary ingredients and independently mix them.
To obtain a good result, the most important criterion will be the use of the correct proportions of the components that make up the composition.
Preparing to knead the solution, it is necessary to prepare a metal or plastic container, in which all the ingredients can be mixed. With the help of a shovel shovel, it will be convenient to pour all the components into the container and mix them.
Using the trowel will allow you to apply the ready-made mortar to the surface, but you can also knead a small amount of the substance with it if you need to cover only a few cracks.
At the first stage of preparation it is necessary to work only with sand and cement, which must be well mixed with each other. The choice of proportions in this case depends only on the brand of cement to be elected.
The resulting cement plaster will be divided into the following brands:
- M200 with a mark of 200 it will have a sand and cement ratio of 1: 1, with a mark of 150 it will be 1: 2.5, for 100 it will be 1: 3.5, and for 75 - 1: 4;
- M400 at mark 200, the ratio of sand to cement will be 1: 2, at 150 it will be 1: 3, at 100 - 1: 4.5, and at 75 it will be 1: 5.5;
- M500 with the mark 200, the ratio of sand and cement will be 1: 3, for 150 it will be 1: 4, for 100 - 1: 5.5, and for 75 - 1: 7.
In order to make a quality solution, the first thing worth doing sand. It is sifted through a sieve.to exclude any inclusions. Cement should be relatively fresh, because working with stale residues can be problematic. If there is no choice, then it is also sifted like sand, so that you can remove the hardened areas and leave only one-component composition. In this case, the proportion of sand is reduced by ¼ due to the unusual characteristics of cement.
A complete solution can be prepared using water, which is poured in after the complete mixing of the dry elements. It is necessary to pour in slowly and in parts, after each of them mix everything thoroughly, preventing the material from grappling and hardening.
In order to dissolve such a mixture, only water is not always enough, often it is necessary to add a plasticizer to it.
There is another option, as you can make a cement-sand mixture, but it involves the reverse sequence of actions. First of all, water is collected, the amount of which in the tank should be 4/5 of the required volume. After this, liquid soap or another detergent is added, which foams to the maximum.Only after that you need to fill up half the volume of sand and all the necessary cement into the working tank. All contents are mixed until a homogeneous mass.
The next step will be the addition of the remaining sand, after which the solution should be stirred until it is completely homogeneous. It is very important that the cement with sand is very well mixed.Otherwise, the result of working with him will be disappointing. Using this option, it is possible to mix the components more efficiently and to obtain the optimal composition, rather than with dry mixing. Important during the final batch add some waterwhich will give the chance to receive solution of the necessary consistence.
It is important to ensure that the finished product does not stick to the paddle and does not flow down from it like water, for which the correct ratio of all components should be used. Neglect of this rule will lead to an incorrect final batch result, which will entail poor-quality work.
Instruments
In order to prepare a cement-sand mortar, it is not necessary to have a large arsenal of tools that will be useful in the work.The most basic is the capacity in which the composition will be kneaded. You can use a metal or plastic bowl, bucket or tray. A more professional option is the use of a mortar or concrete mixer that allows you to mix components more efficiently. If these devices are also electric, they can constantly mix the contents on their own, which will not allow it to quickly freeze.
Choosing the right capacity for kneading, it is better to give preference to products of round or oval shape that do not have corners.. It is in them that often remain unmixed parts of a component, which leads to a violation of the total mass of the substance.
In order to conveniently pour sand and cement into the pallet, especially if the work front is to be large, then you need to have a shovel, better a shovel, for ease of use. In the creation of cement-sand mortar, you must precisely observe the proportions, and therefore it is necessary to have a capacity that allows them to be measured. The easiest way will be a bucket, it will help pour the required amount of sand, cement and fill the required amount of water.
If there are no specialized construction tools on hand, the composition is mixed with a wooden oar., which should have optimal dimensions, taking into account the capacity in which the mixing takes place. If the technical equipment is at a high level, then with the help of a drill, into which a special nozzle or a construction pistol is inserted, it is possible to mix all the parts qualitatively, obtaining the desired result.
Also useful is the construction cone, with which you can easily determine the mobility of the solution. Having prepared all these materials, you can begin repairs.
Proportions and additives
Depending on what exactly you need to prepare a cement-sand mortar, it is important to choose the right amount of all components. If it is necessary to make brickwork, then cement and sand are mixed in a ratio of 1: 4. The ratio can vary not only depending on the type of cement, but also on the choice of material to be dealt with. For brick 75, it is better to mix 75 grades, for which cement with sand and water is taken in a 1: 5: 3 ratio.
If you need to do tile laying, then cement, sand and water are taken in the ratio of 1: 2.4: 0.4.In the process of preparing the composition, it is important to be careful and pay attention to the mass that is obtained. Do not rush to pour in all the water, because the sand may be wet and the resulting solution will be too liquid.
If you apply a small amount to the tile on the side where the solution will be, by turning it over you can check whether the composition is ready. If the mixture drains, the composition is too liquid, if the mass is completely behind the surface, then it is heavy. Ideally, if the layer deposited on the surface remains on it. In order to provide better adhesion to the mortar, it is necessary to make cement milk, which requires water and cement in the ratio of 3: 1.
To the cement composition was plastic for a long time, it is possible to make a variety of additives, called plasticizers. Such solutions should also be made with all necessary proportions.
Additives that are made in the cement-sand mixture can be:
- Slaked limewhich can have three states depending on the amount of water in it is fluff, where 75% is calcium oxide and 25% is water; lime paste and lime water - a small amount of lime dissolved in water.The process of slaking lime must begin no less than two weeks before the construction work is carried out, otherwise the resulting mixture may be deformed. If you add hydrated lime in the cement-sand mortar, it will have the best indicators of vapor permeability and strength.
- Use of PVA glue. It helps to improve the adhesive properties of the mixture and give it elasticity, which is very important for plastering surfaces.
- Dishwashing detergent or liquid soapwhich helps the mixture to give greater elasticity. It is necessary to add it after water has been poured in an amount not exceeding 100 grams, otherwise the resulting solution will be excessively foamed. The addition of such a tool will allow you to lay a layer of plaster smoother and easier.
- Liquid glass to improve the waterproofing properties, which is useful in the preparation of moisture resistant plaster. This composition can be used for coating stoves, fireplaces and even chimneys.
- Use of carbon black or graphite helps to paint the cement mixture and give it a different shade.
With the help of additives, it is possible to increase the amount of the substance itself,which seems insignificant in a single batch, but in one cube of the solution it will have very different indicators, which will give a small savings. Knowing what can be added to the solution to obtain certain characteristics, it is possible to make the process of surface treatment more comfortable, and the result is several times better.
Tips and tricks
When working with cement-sand mortar, it is important to use only clean tools, so that no residues from past work or dirt get into the finished mixture. After the completion of work or the process of kneading itself, all equipment must also be thoroughly washed. So that parts of the mixture do not stick to the working tools, it is important to wet them all the time with water.
The finished solution after mixing begins to harden and it has to constantly interfere. To avoid this, you can pour a little detergent into the water. It is this component that gives the mass plasticity and does not allow it to quickly harden, which makes the work more comfortable.
If construction work is carried out in cold weather or in winter, then potash must be added to protect the mortar from drying and cracking.With it, you can protect against the effects of low temperature, while not spending a lot of money. As for backfill, for such a solution is not terrible frost to minus ten, and if necessary, you can also add potash. In cold conditions, most problems with sand, because it can freeze. It is recommended to store in rooms and to warm up if necessary.
Water in the case of construction in the cold is also used warm. With its help, you can make a warm solution that will cool for a longer time, which means it will retain its plastic qualities and properties. In warm water it is easier to dissolve the detergent, which will prolong the working capacity of the cement slurry even longer.
Each type of work has its own nuances and secrets that you need to know in order to quickly and easily cope with the task. Cement-sand mortars are very popular because they are used in a wide variety of types of work, which means that any man in the street or a professional has had to deal with it. The success of its application depends on how accurately the proportions in the preparation were maintained and whether the construction technology was respected.
In this video, you will find a master class on the mixing of cement-sand mortar for plaster walls.