Screed floor: the details of the process and technology features
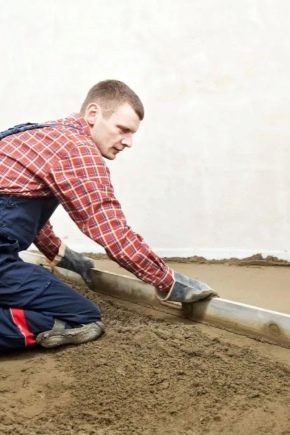
What is a floor screed, not everyone knows. It is a necessary element of construction or major repairs and performs a number of important functions. The main purpose of the screed is leveling the floor, making it stiff and hiding utilities. For systems such as underfloor heating, the screed also has a protective function. In addition to the main purpose, the screed is necessary to increase the insulation of the room. It prevents the loss of heat through the lower floors and increases the level of comfort of living due to noise insulation properties.
To equip the floor screed is important and necessary, but its installation is complicated and requires some skills.It is important to know the details of the process and the features of the wet, semi-dry or dry screed technology, depending on which type of screed was chosen.
Kinds
The construction market today offers several types of screeds, which are conventionally divided into several categories: by component composition, by adhesion method, by installation method, by purpose.
According to the composition of the material
The composition of the material is directly affected by the type of screed: wet, semi-dry or dry. At the same time, in the same row with wet (liquid) it is necessary to consider leveling mixtures with self-leveling technology.
Wet screed is considered "ageless classics" in construction. It turns out good-quality, solid and durable due to the components in the composition, securely adhering with water and harden in air.
Wet screed options are many:
- Cement. A simple and reliable mixture of cement and alluvial river sand when added to water forms a mass of consistency that is convenient for pouring, quickly hardens and serves for many years. For the price, such a screed refers to cheap, and in terms of performance - to one of the most reliable;
- Concrete. In composition, it is similar to cement, since it is based on synthetic binder and alluvial river sand that has undergone various treatments. Rubble may also be present. Popular clay ties ceramsite;
- Mosaic. At its core, it is a concrete screed without rubble, but with the addition of polymers and polymer cement. As a decorative component, marble and granite chips, colored claydite-concrete and other substances are introduced into the composition;
- Anhydrite. It has a fundamental difference from the texture of a concrete or cement screed. Anhydride is a “dehydrated” gypsum and upon subsequent addition of the liquid turns into a homogeneous pliable mass, which resembles a self-leveling floor rather than a rough concrete screed. It does not require additional efforts to reinforce and level the floor surface, but does not allow making the thickness sufficiently large. The best option - 25-35 millimeters;
- Asphalt. It is made from a binder and a dry mixture of small fraction. Performance characteristics of asphalt screed at a heightsince it is very wear-resistant (unlike the same plaster), it does an excellent job with sound insulation and heat insulation and does not contain any substances harmful to health;
- Synthetic. Such a mixture implies the presence of synthetic fibers or plastic reinforcing the screed. Additional components make it strong, like reinforced concrete, but less heavy;
- Mortar or leveling. These are ready-mix based on gypsum with the addition of various fibers, metals and binders.
In a separate category will stand the self-leveling floor. It is used in cases where the surface of the subfloor is not in a deplorable state or as a topcoat for a concrete screed. Bulk screed is more suitable for self-use without the help of a professional, gives a good result, but at a cost several times higher than a cement or concrete screed. Its maximum height is 30 mm.
A semi-dry screed, suitable for fast work on a relatively flat floor surface, most of them have the same composition. Different manufacturers of different types of plasticizers and the proportions of the components.There are 4 of them in total: coarse sand, cement powder, polypropylene fibers, plasticizers. When preparing the mixture water is added, but in smaller quantities than for liquid screed.
Semi-dry screed does not require reinforcement and additional protection, since the fibers in the composition are intended to increase ductility and strength.
Dry screed is a more modern way.
It is a layered alternation of materials:
- Polymer film required to protect against moisture and condensation.
- Damping tape Also called edgeband.
- Beacons and guides that regulate the uniform distribution of the substance over the floor area.
- Leveling layer Substance for dry filling, which consists of the main part and thickness of the screed.
- Sheet or slab material, leveling the surface of the bulk layer.
- Protective PVC film, which covers the hydrophobic leveling sheets;
- Mastic, glue and screws for joining sheets.
The composition of the dry screed varies substance for dry backfilling. Most of its species do not require professional intervention.
Varieties of dry screed components:
- Sand based blends. Most often they consist of alluvial river or quarry sand and cement. Sometimes there are other components in the composition to improve the absorbent properties and increase the wear resistance of the abrasive substance. The sand that has undergone several processing procedures and has been cleared of living organisms and impurities has several advantages: it does not “sink” over time, it allows you to do the work quickly and cleanly. It is an eco-friendly product of organic origin.
- Concrete mixes. With the addition of gypsum, sand and expanded clay.
- Slag backfill. Despite existing prejudices about the use of slag in a residential area, this material consists solely of natural components. It perfectly copes with its task as a dry screed and is distinguished by low cost, since slag is a production waste. There are also several types of it:
- Domain. Very similar in its properties to cement mixtures, but less hydrophobic and more frost-resistant;
- Mineral wool. This is not slag in its pure form. Mineral wool is produced by heat treatment of slag from metallurgical production.
- Coal. Suitable for use in all types of screeds. Differs in cheapness and optimum structure;
- Fuel. It is kept for 3 months in shtrob, and then used for mounting screed with high insulation performance.
- Expanded clay. It is used in its pure form, since this low-melting clay after heat treatment already has all the necessary properties: low weight, low cost, organic composition, ease of installation work.
- Perlite. The sand grains of volcanic origin, "swollen" by calcining in a furnace to a light porous state, are used as expanded clay.
- Vermiculite Unites in itself qualities of two previous porous materials, but costs a little more expensive.
- Plates based on cement and wood fibers. They are durable, smooth, even, do not require additional efforts during installation, are not afraid of moisture, are biostable, do not freeze through, weigh a little, are easy to install, and are cheap.
By way of clutch
It is customary to distinguish 4 types of coupling couplings with the base:
Bound
This type of screed got its name due to the fact that the liquid mixture directly binds or adheres to the surface of the subfloor without the use of any cushioning material.Filling turns out solid, durable, wear-resistant, but fraught with difficulties.
First, for good grip, you need to add a lot of water. This creates the risk that the mixture will leak to the neighbors. Secondly, the screed shrinks heavily after evaporation. This can significantly reduce its width. In addition, water "stretches" the substance, and when it hardens, cracks appear on the surface. Drying is uneven and one part of the screed can sink more deeply than the other. Such a screed is especially dangerous when it is poured over a water-heated floor.
It is necessary under the following conditions:
- Large differences in floor height;
- Low ceilings, for example, in the “Khrushchev”, which do not allow a high line of the floor;
- The need to install a durable and durable coating.
On a separating layer or substrate
From the name it is clear that this screed is devoid of adhesion (adhesion) with the surface of the subfloor in the room. Between the layer of liquid mixture or dry fill is a thin polymer film. It is necessary in damp rooms and at risk of condensation.Also, the substrate helps to protect the wooden floor from the "exhaustion" of moisture from the liquid screed. If the liquid will evaporate from it in an accelerated mode, the screed will crack, and the wooden flooring may start to rot.
"Floating"
Such a screed is inherently close to a multi-layer dry screed and is a modified version of casting or backfilling on a substrate. The principal difference is that in addition to the moisture-proof film, a layer of insulating material is also placed, which prevents heat loss and increases protection against noise in the room. This screed due to the number of layers increases in thickness from 30 to 40-50 mm.
Reasons for use:
- Poor floor performance;
- The presence of a heated floor system;
- Ground floor apartment building with a basement below or without;
- For further finishing requires the most even floor;
- The budget is limited;
- The finish will be soft: linoleum, carpet, laminate.
Team or leveling
In the construction of this type there are no bulk and liquid elements. It consists of layers or roll materials that provide protection from moisture, noise, cold and are mounted with adhesive adhesives with one-piece plates.
Combined screed is necessary in cases where the draft floor is sufficiently dry and level, and installation work must be carried out quickly.
By way of laying
Here again, the already familiar division of varieties into solid (wet), semi-dry and leveling screeds is used.
The solid is leveled manually, for a semi-dry a special machine is needed for kneading and tamping the material, and the leveling mixtures are leveled under their own weight without additional manipulations.
To destination
A screed is a multifunctional coating.
It is necessary in such situations:
- Leveling the floor surface. At construction of any building wooden or reinforced concrete overlappings are used. Despite the massive nature of their production, they are not absolutely identical. One slab may differ from one another in thickness, width and length. Moreover, these indicators sometimes differ when measuring one plate at different points. As a result, the overlap has noticeable joints, depressions and irregularities, on which no type of finishing will lie. To align the subfloor any technology is suitable, be it a fill,At the heart of which is concrete, or dry backfill of expanded clay. The nuances of choice depend on the location of the room and its microclimate.
- Creating an incline. This option is less common. As a rule, a sloping floor is required in large showers and rooms where there is a drain. Due to the high humidity and features of an inclined screed, only liquid mixtures can be used for such work.
- Surface preparation for flooring installation. Here we are also talking about leveling, but with different goals: to laminate lay perfectly, so that there is no crease on the linoleum, in order to reduce the consumption of glue when finishing tiles.
- The need to block engineering communications and heating systems. Here are relevant all types of screed, except for the national team. For the water floor is more suitable liquid, for the film - leveling mixture. In this case, the screed simultaneously aligns the surface above the heating system and protects the system itself from moisture and damage.
- Enhance thermal insulation in the room. Such an application screed is important for country houses, villas, apartments on the first floor, which are colder than others because of the proximity to the ground.
- Improving sound insulation in the room. From the neighbors above and to the side, the screed does not save, but the sounds from below are not audible at all. And the neighbors do not have complaints about the jumping children, running around the apartment of pets and the untimely rearrangement of furniture.
Advantages and disadvantages
Each type of screed has its own characteristics, advantages and disadvantages.
Pluses wet screed:
- Able to level any floor, even if its surface is in a very poor condition;
- Suitable for creating sloping surfaces in washers, showers and garages. It is necessary in premises for the organization of discharge;
- Thorough, reliable, wear-resistant screed, which is widely used even in industrial premises;
- Materials are not costly;
- It can be used to level the floor along the laid contour of a warm floor;
- It creates an excellent sound insulation layer;
- Some varieties can serve both as a rough finish and as a topcoat.
Cons wet screed:
- Assembling it is time consuming and complex, it can not be done without the help of professionals;
- A special technique is required for mixing the mixture and leveling the surface;
- The work is dirty, there is a risk that the mixture will leak to the neighbors;
- Concrete or cement screed is very heavy, gives a large load on the floor;
- Cold on its own;
- Time for complete drying of the screed - 28 days;
- It may shrink after evaporation of moisture, which will lead to the appearance of cracks on the surface and the risk of damage to the heated floor under the screed.
A separate type of liquid screed - leveling mixture or self-leveling floor.
Its advantages:
- It weighs less than a concrete screed;
- Prost in work, does not demand intervention of the expert. To level the surface of the floor, it is enough to follow the instructions from the manufacturer;
- Does not leave dirt and dust, not so thick as to flow to the neighbors;
- No special mixing technique required;
- The mixture is self-leveling, that is, it takes the desired shape under the weight of its own weight;
- Serves as a decorative coating at the same time, maybe with a pattern;
- It dries several times faster;
- The ideal base for any type of flooring;
- Protects electric and infrared floor heating;
- Promotes increase of thermal insulation and sound insulation in the house;
- Not afraid of moisture.
Its disadvantages are:
- The surface of the floor should be relatively flat and clean. With difficult cases, the mixture can not cope;
- The maximum layer height is 30 millimeters. This is not always enough for a screed;
- High material consumption at a very high price.
The semi-dry screed deserves attention due to its advantages:
- A small amount of water solves the problem with the leakage of the mixture to the neighbors. They just do not happen;
- The reduction of the liquid in the composition by 3-4 times also shortens the time for drying the screed;
- Virtually no shrinkage;
- Does not crack after drying;
- It is cheaper than liquid analogues;
- Durable and reliable;
- It is combined with a contour of a heat-insulated floor;
- Increases the level of comfort in the room;
- Consists of environmentally friendly components.
But it has several disadvantages:
- The coating is hydrophobic. Prohibited for use in wet areas;
- It will cope better with the alignment of a relatively smooth floor in a new building than when re-mounting the screed on a very uneven floor surface in an old house;
- Requires special equipment for installation;
- The minimum height is 40 millimeters. For rooms with low ceilings, this is critical.
The technology of dry screed conquers more and more fans thanks to an impressive list of advantages:
- Well manifested itself in operation in different types of premises, from living rooms in an apartment to outbuildings in the country. This is achieved due to the fact that the dry backfill is porous and resistant to freezing;
- The easiest of all types of screed. The low weight of the whole structure allows the use of a coupler even on weak floors;
- More suitable for leveling wooden flooring;
- Copes with the most difficult types of overlappings;
- In the process, there is no excess dust and dirt;
- You can do it yourself;
- The mixture does not freeze, so the procedure can be interrupted and restarted;
- Components are of natural origin, harmless even in the nursery;
- It is easily combined with different types of floor heating systems;
- You do not need special equipment, only beacons and guides, which are bundled from the manufacturer;
- Almost does not settle, does not crack;
- Maximum increases the level of noise insulation and prevents heat loss;
- Drying and shrinkage time - up to 4 days, then you can continue to repair;
- Upper sheet material makes the surface of the subfloor perfectly flat;
- The term of operation is more than 20 years.
The technology is also not without cons:
- Dry backfill is not a monolithic formation. With an insufficiently dense layer, larger abrasive particles rise to the top, and small particles settle down, causing the screed to "sit down";
- When combined with a warm water floor, there is a risk that the pipes will taper and heat up too much, this will lead to their displacement, since it does not give a rigid fixation;
- When using flooring without a stabilizing layer (carpet and soft), significant point loads can make the coupler uneven;
- On earthy surfaces, it requires an additional layer of insulation;
- Abrasive particles wear out;
- Many types of dry fill are hydrophobic;
- Organic matter is an excellent breeding ground for fungi and bacteria. If the screed gets wet, problems may arise over time.
Factors Affecting Choice
The choice of a suitable screed regulates a number of conditions. First of all, the type of room is important: a private house or apartment, the first floor, or from the second or higher, you need to warm the floors in the house or in the utility room.
Any type of screed is suitable for first floors if it is floating, since this floor is the coldest and the risks of condensation under the floor are the highest. Concrete and cement screed, expanded clay aggregates and variations of vermiculite and polystyrene concrete work well in exploitation.
PVC film works best as a waterproofing, and mineral wool can serve as a heater.
Next, you need to assess the type of overlap. Concrete slabs without any problems coexist with concrete, cement, expanded clay, various slags and plasticizers. But the boards are more capricious in choosing the material for the screed. Liquid mixtures based on cement, concrete, and water may be too heavy for them and too much moisture in the wood fiber. To dry this screed will be very long.
Affects the choice of purpose screed. If this is only the alignment of the floor, you can limit the concrete. Backing is suitable for insulation. Sound insulation will improve in any of these cases.
Not the last role is played by the operational state of the floors. Strong constructions will withstand a lot of liquid and semi-liquid screeds, but for the weak it is better to choose a dry screed or bulk mix.
It does not hurt to take into account the maximum difference in floor height. Concrete screed is able to align up to 50 millimeters, the rest of the indicators less. The most even floor without serious defects and has a dry-pouring screed, and different types of backfill, and the team of plates, and quick-drying plaster, and self-leveling solution.
When choosing for premises of various functional purposes (kitchen, recreation area, bathroom and others), one of the main criteria is resistance to moisture. The leader among the species is a continuous screed, in the second place is dry-grained, and is most susceptible to a wet microclimate, which means that a dry screed is less suitable. An exception is the sheet material of cement and wood fiber. Such plates are not related to hydrophobic.
A less common reason to choose one option or another is temporary resources. If the repair does not tolerate delay, then the best option - a team screed of plate material. In the presence of time from week to crescent, it is important to use a semi-dry and dry screed. When deadlines are not tight, you can spend time installing wet. It will take a month or more, given the time it takes to dry completely.
Financial capabilities are also important. Estimates should take into account that during the "wet" work will need to purchase or rent a special fixture, equipment and hire workers. Plus the cost of materials. With a semi-dry screed, the costs are similar. Dry screed does not imply such work, the work can be done independently, but the materials supplied to the market are a monopolist brand, and the complete set will cost a round sum.
Of course, you need to pay attention to the advantages and disadvantages, strength, performance characteristics in the documentation and the availability of the documentation itself.
Careful examination of the issue will save you from an error in the choice and possible problems in the future.
Process features
Distinctive features of the technology laid in their name. Accordingly, a wet floor screed in an apartment implies working with liquid compounds and pouring, and a semi-dry and dry one with crumbly substances.
Filling of continuous screed on the basis of various cement-concrete-plaster combinations, sand and fibers occurs in several stages:
- Disassembly work. They involve a thorough cleaning of the rough surface.It is necessary to get rid of construction debris, fill up the gap filler. Not to the absolute ideal, but the cleaner the floor, the better the grip.
- Processing of overlapping priming composition. The primer improves biostability and improves the bond of the floor with the tie;
- Marking on the walls. Here the laser level is used so that the lines are strictly horizontal, and the surface of the screed is as flat as possible.
- Laying waterproof PVC film if necessary. It can also be bituminous paper or other sheet material that can be laid overlap to 25 centimeters. The edges should go on the wall. Waterproofing is necessary in damp and cold rooms, and can also protect against leakage of the liquid mixture to the lower floor.
- Installation of damping tape. They pasted the bottom edge of the wall along the entire height of the leveling layer before it is poured. Edge tape fixes waterproofing material.
- Laying insulating materials if necessary.
- Installation of beacons. Lighthouses are a kind of metal grid with a big step. They are a guideline for calculating thickness, surplus is removed and the surface is leveled.
- Preparation of the solution. The choice of method depends on time, skills and financial capabilities.
- Fill Correctly start from the wall opposite the doorway. The solution is laid out in portions and is aligned with the beacons. After pouring, it must be left for 4 weeks until completely dry.
The self-leveling floor technology is somewhat simpler, but is only suitable for the most even surfaces.
It includes the following steps:
- Cleaning and degreasing floor space. There should be no dust, traces of paint, grease stains and other defects that interfere with the quality of adhesion of the mixture to the floor.
- Primer. Concrete contact is also suitable. These substances give the rough floor a rough surface for good adhesion and protect against the appearance of fungi and microorganisms.
- Creating a suitable indoor climate. The room is isolated from drafts, a comfortable temperature for the mixture to harden is 5-25 degrees.
- Dilution of the mixture in a large container with water and a construction mixer. The consistency should be uniform, without lumps, not too thin.
- Applying the mixture to the floor surface. This is done with a needle roller with a long handle and a trowel. The mixture is poured in portions and “rolled”, and then independently takes the desired shape.
- Drying period - up to 2-3 days.
The technology of semi-dry screed, as well as other species, happens with and without reinforcement. Reinforcement involves the installation of the grid to give the tie stiffness. Installation of additional layers for stabilization of the mixture, waterproofing and noise insulation can also be carried out.
In the process of work there are several distinctive features. The first few stages are recommended to be performed in the same sequence as for the wet screed: surface preparation, primer, reinforcement (if needed), installation of a damper tape, preparation of the solution.
In order to prepare and serve the solution, a special technique is needed, therefore a semi-dry screed is difficult to perform without the participation of professionals.
When the solution is ready, it should immediately begin to lay. The first layer is 15-20 mm, then put a reinforcing mesh on it. It is optimal to weld mesh fragments together, but wire can also be used. Then pour another 20-40 mm solution. If there are fibers in its composition, the reinforcement is not necessary.
Then the surface of the solution is leveled. This requires beacons, guides or sheets of drywall, a laser level and an instrument called the rule.
The next stage is grouting.It occurs at the moment when the mixture “grasps” a bit and profiles can be taken out of it. Traces of the profiles are filled with mortar, and then the entire surface is polished with a construction grinder.
Care for the screed is also part of the process. It is not enough just to leave it for a few days until completely dry. Since there is not too much water in it, it evaporates very quickly and the screed may freeze properly. To prevent accelerated evaporation, it is covered with polyethylene on top or create a wet microclimate in the room. Dry screed from 4 days.
Fundamentally different from previous types of technology team or dry screed. It consists of a large number of layers, each of which is important and necessary and affects the quality of floor operation.
The course of work is performed in the sequence recommended by the manufacturer:
- Preparatory work. The surface of the floor is dried, dedusted, treated with spatula solution in places with pronounced cracks and defects. The joints between the floors and in the joints of the walls with the overlapping must be sealed with a soft material, for example, mineral wool.
- Primer.This step is necessary when working with bulk materials, since they are of natural origin and are more susceptible to the appearance of living organisms and fungi.
- Leveling layer Not always required, but only in cases where the overlap is in very poor condition. Height differences, chips and problem areas that are not able to level the dry backfill, treated with cement mortar or a mixture for self-leveling floor. The frozen even layer needs secondary preparation: dust removal, primer.
- Determining the height of the tie when using a laser or water level.
- Installation of waterproofing and vapor proofing materials for those rooms where it is impossible to influence the increased level of humidity. For concrete, block, cement base layer of the film is used, stacked overlap and calling on the wall. For a wooden floor, bituminous paper or paraffin paper is more suitable. A portion of the insulating material that extends over the wall to the full height of the future screed is glued with edging tape. This simultaneously keeps sheets and protects walls from cracking.
- Thermal insulation and soundproofing.It implies the installation of sheet material, but not always required. The dry-bed layer itself copes with the functions of the insulating substance.
- Installation of lighthouses and barriers at the exit from the room (for all doorways, if the room is through). Backfilling has a "fluidity", therefore, at the border of the premises temporary thresholds are set according to the level of the screed height. Beacons and guides are installed according to the scheme.
- Backfilling. Strict rules for laying abrasive material does not exist, but it is important to observe the density recommended by the manufacturer per square meter and equalize simultaneously with the falling asleep material. For the construction of beacons for this purpose, a rail is provided, which “walks” along the guides and aligns the upper layer of the screed.
- Overlap installation. The peculiarity of the dry backfill is that it is necessary to cover the top with sheet material in 1 or 2 layers in order to reduce the point loads and subsidence of the substance. The layers of gypsum-fiber sheets are interconnected with mastic and screws. The seams are rubbed to a smooth surface. Then you need to leave a tie for natural shrinkage. The approximate drying time is from 3 to 5 days.
Materials and tools
All the necessary equipment and materials used can be divided into two groups: universal (necessary for any type of work) and specialized (for a particular type of tie).
Universal materials and tools:
- Devices for dismantling of old finishing materials. The kit itself may be different, from the nail puller to remove the plank flooring to the B52 paint shredder. You may also need a spatula to remove old paint, brushes and a hair dryer. Tiles, as a rule, have to prick or clean parts. For this you need a hammer drill, chisel or metal hooks. In a new building, private or multi-family panel house things are easier. It is only necessary to remove debris from the ceilings, dust the work surface with a building or ordinary vacuum cleaner and wash it with water with soap.
- Do not forget about the precautions. Installation works in dusty and dirty rooms, and small fragments of tile or paint solution can damage the skin of your hands, so you need working equipment - closed clothes, high heel shoes, rubber and cotton gloves, a respirator and plastic glasses.
- Priming compositions.Concrete contact is excellent for concrete floors, universal primer and wood treatment liquid are suitable for wooden floors. A primer is applied with a paint brush (preferably synthetic, it absorbs less of the product) or with a roller.
- One of the first necessary tools is the building level. Levels can be of different types: flask, water, laser. The most accurate is the laser level, but in the hands of a professional, the flask can be quite accurate.
- A level-related tool is a metal profile or "plaster beacon." It also happens wooden. An alternative option to purchase a lighthouse - cement-sand beacons, which are made independently and are placed around the perimeter of the room. But this option in order to save is only suitable for those who have extra time to wait until they dry out. Approximate period - 3 days.
- If it is necessary to install additional layers, the list of materials and tools is replenished with film and heat insulation sheets. PVC, bitumen paper and other waterproofing layers are purchased in rolls at the rate of floor area plus 25% for overlaps. Between themselves are connected with mounting tape.Insulating layers are also sheet or slab. To cut the material into fragments, use a sharp construction knife.
- Mandatory element - damper or edging tape. It is easier to cut with scissors, so that they, too, better stock up in advance.
- Aluminum rule. It is a lightweight, durable, convenient tool needed for laying out and leveling a liquid or semi-dry mixture. This device is inexpensive, but better than any other tool copes with leveling the surface of the screed.
- Plastering trowel or trowel. It is necessary for mashing the surface of the screed to achieve maximum smoothness.
In addition to patience (screeds dry for about a month), specialized materials and tools are needed for wet and semi-dry varieties:
- Ready mix in liquid form and concrete pump for its supply, ready dry mix and water or dry ingredients for mixing and dilution with water;
- Capacity from 30 liters in volume, measured capacity for water;
- Grinder;
- Construction mixer. Also use a drill with a nozzle for mixing liquid substances.
Devices for a bulk floor:
- Calculator for mathematical calculations to accurately determine the consumption of matter per square meter. If in the case of cement the exact value is not critical, then the self-leveling floor is too expensive to overpay for the extra kilos of the mixture;
- Capacity with high walls;
- Electric drill with a mixing nozzle;
- Notched trowel from 50 to 100 cm wide to align the surface of the screed;
- Needle roller with long handle. It simultaneously helps to distribute the composition on the floor surface and pierces the bubbles formed in the mixture.
The required set of additional tools for mounting dry screed:
- Material for processing joints: wood fiber, mineral wool, mounting tape;
- Backfill material. One of the most common is keramsit. It allows you to avoid unnecessary spending on materials for the installation of insulation and sound insulation in the room. The approximate consumption of material is 40 liters per square meter, and the weight of the screed is 3 times less wet or semi-dry;
- Sheet material for leveling the surface. This is usually gypsum fiber;
- Mastic or glue for bonding gypsum fiber layers;
- Spatula to remove excess mastic;
- Drill and screws.
What should be the thickness?
Leveling the floor does not occur by eye. The thickness and density of the screed is calculated depending on the state of the overlap and the desired result. Also it is necessary to take into account the type of room, soil, the presence of the contour of the heated floor and its type, the maximum load on the floor surface.
Screed less than 20 millimeters in height does not happen. This is the minimum value for leveling and self-leveling mixtures, suitable for different types of premises and combination with an electric heated floor up to 5 mm high.
The minimum height that can be filled with liquid mixtures is 3 mm. Otherwise, it just cracks. A layer above 40 mm is needed for rooms with high loads and high traffic. It is better to reinforce this screed, then its height will be from 5 to 7 cm. It also adds centimeters and additional insulation. And if PVC film is only 1 mm, then polystyrene concrete is much thicker.
Screed less than 4 cm will be short-lived and fragile
The thickness of the screed for leveling the surface above the contour of the underfloor heating can be up to 10 cm. In this case, it is permissible to use wet and semi-dry screeds only when the floors are in excellent condition.If their operational evaluation raises doubts, it is dangerous to fill in such a floor with cement, sand concrete or gypsum. It is preferable to dry option. Lightweight backfilling weighs 3 times less, so its layer can reach 10-15 cm. The exception is the floor in the “Khrushchev”. In buildings of this type, the ceiling is rarely quite high, so you should limit yourself to the minimum thickness of the screed.
Surface preparation
The preparatory phase of the screed is important. To reduce the number of actions for warming, priming, leveling and protecting the working surface from moisture helps universal building material - penoplex. Penoplex is called cellular polystyrene, which can be of several types: for roofing, walls, floors, and outdoor areas.
All varieties have similar benefits:
- Low weight;
- Porous structure;
- Increased strength;
- Moisture resistance;
- Preventing heat loss indoors;
- Long service life.
The installation of the foam plaster on the work surface simplifies the filling of the screed or the formation of the bulk layer, as the sub-floor becomes as smooth and suitable for installation as possible.
Lighthouse system and reinforcement
These are two independent procedures. But if reinforcement is needed far from always, then the installation of beacons is an obligatory stage of the device of a coupler of any type.
Reinforcement is, in fact, a gasket made of metal in the body of the screed, which protects the heating system from the severity of the leveling layer of the floor, prevents it from cracking and increases strength.
It is necessary when the floating screed (done when the floor is close to the ground), there is no fiberglass in the composition and the layer thickness exceeds 4 cm. In other cases, the procedure can be avoided.
Beacons are installed directly on the reinforcing mesh. There are two types: Reiki and rappers.
Reiki, in turn, are divided into several varieties:
- From the tree. This is an affordable and easy-to-use type of beacon with several features. Firstly, it must be well soaked in water before use so that the wood does not absorb moisture from the screed itself, and secondly, the tree must be removed, otherwise it will rot inside the cement layer over the years;
- From the profile. "Plaster beacon" is suitable for pouring or filling screed up to 30 millimeters.With a greater thickness, it will simply bend under the weight of the screed and will cease to perform its function;
- From the pipe. Can be with round, rectangular, square section. Used for mounting on large areas for thicker screed;
- From the solution. The basis of the lighthouse is a steel thread, which rests on the screws. A solution is applied over the thread, which subsequently becomes a reference point in a straight line;
- From the solution in the form of a slide. Such landmarks are placed along the entire perimeter of the floor at the same height. The width between them should not exceed the width of the aluminum rule. That is, the minimum is 50 cm, the maximum is 100.
Preparation of the solution
There are 3 proven ways to get a solution:
- Delivery of ready mix to order or making it by professionals before work begins. In this case, the mixture is prepared outside the house. All bulk components and water are mixed in construction equipment that combines the function of a concrete mixer and a concrete pump. For large diameter hoses, the finished mixture is fed to the height of the third floor. This eliminates the need to carry heavy containers with the mixture to the house, makes the work cleaner, and the mixture slows to harden.But this is the most expensive and time consuming method. You must pay for the services of the construction team and rental equipment.
- Purchase ready mix in dry form. Cheaper than the first option, but for its preparation will need a large capacity and construction mixer. From time to time, the mixture should be mixed in as it hardens quickly. A little to extend the time in which it will remain liquid, will help the film covering the tank with the solution from above. In the finished form is purchased mixture for the liquid screed and dry-pressed mixture. Also in the bags for sale dry filling of expanded clay, polystyrene foam concrete, various mixtures with foam concrete, but they do not need to be diluted with water at all.
- Purchase of all components separately and preparing the solution with your own hands. This is the cheapest and most difficult option, because you need not lose money with the components for the composition, their ratio and total mass. The most difficult thing here is to choose clean sand and reinforcing fiber. But with the right combination, this screed does not differ in quality from the factory mix.
Fill
Filling in most cases is done manually.It is necessary to level the wet mixture with a roller (if it is a self-leveling floor) or with an aluminum rule, and then wipe it with a trowel. For semi-dry screeds special machines are provided.
A quality screed is necessary in an apartment, country house or cottage so that in the foreseeable future it is not necessary to repeat this complicated procedure during the repair.
With the most even floor surface, several tasks are simplified:
- The floor level becomes a guideline for marking up various objects, such as outlets and switches;
- Simplified finish. The laminate, parquet, tile, soft flooring lays perfectly on an even screed;
- Exactly worth furniture and appliances;
- In the case of self-leveling floor screed is already a decorative finish.
Care Tips
Care for floor screed comes down to one important procedure - do not let it dry out, otherwise the surface will crack.
For this it is important to follow a few rules:
- Do not create drafts indoors;
- Observe the temperature range from 5 to 25 degrees;
- Do not put strain on the screed;
- Spill it with water from time to time;
- Cover with plastic wrap.
Reviews
Screed floor is unanimously recognized as an integral element of the design of the room. Among the advantages, users note that the floor becomes very smooth, the finishing material easily lays down on it, noise is muffled, the room becomes warmer and more comfortable to be.
Negative reviews are also found. Among them - the complexity of the work, the high cost of some materials, the coldness of the concrete floor.
On how to properly make a cement-sand screed, see below.