What can putty drywall?
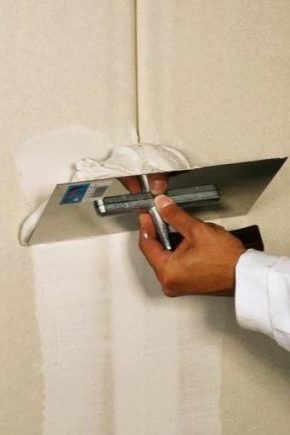
When finishing plasterboard sheets, there are a number of characteristic problems that must be putty. These features include: seams, cracks and joints, formed in places of transition from sheet to sheet. Due to its low strength, gypsum plasterboard can contain various chips, gouges, cracks and other defects that deteriorate the surface quality. Microorganisms can get into them, which will further lead to damage to the finish coating.
To avoid various problems during operation, it is worth using the correct putty for processing. It is important to consider the features of the coating on which the finish is applied, as well as the factors affecting it.
Features of putty compounds for gypsum plasterboard
To choose the right filler mixture, you need to adhere to a certain order of criteria. It is important to understand for what work is putty. If the finish is produced indoors, it makes no sense to buy a mixture for outdoor work. In addition, it is important to determine the type of filler: it can be starting, finishing or universal.
The performance properties that the putty should conform to (surface smoothness, color, plasticity) are important. This also includes the factors that will affect the finished surface (for example, humidity, mechanical loads). It is necessary to consider the shelf life of this finishing material. (it is especially important for ready-made solutions, which quickly lose their properties after dilution or opening of a sealed package).
In addition, the price is important: you must meet the planned budget.
Types of mixtures
Spackling materials are represented by an extensive range of different brands and types. In order to correctly determine the appropriate mixture for putty drywall, you need to understand by what criteria they are divided. There are three main divisions of putty:
- as intended - starting, finishing, universal;
- ready to use - dry mix, diluted solution;
- on the main component in the composition - gypsum, cement, polymer.
Consider the main nuances.
Purpose
Separation of mixtures is carried out by taking into account the size of their particles, which determines the stage for which they are intended, as well as their properties and features.
Starting
This putty is used to align large defects, serves as the basis for finishing putty. Its distinctive features include:
- larger particles of the mixture;
- rough surface;
- strength, complex grinding;
- strong adhesion, strong adhesion to the working surface;
Finish line
This variety is designed to produce a flattened and smoothed plane, it is used mainly on a pretreated base. It is a good basis for various kinds of finishing (for example, pasting wallpaper, staining). The characteristic features of the finishing putty include:
- relatively small particles of the mixture;
- smooth and flat surface after processing;
- nice appearance.
This material can be used as a wall or ceiling decoration. However, this putty is fragile, although it is easy to sand. Handle such coating carefully.
Universal
These fillings perform tasks starting and finishing varieties. Such materials can be used on surfaces in any condition (whether they are almost flat walls or surfaces with cracks, chips and gouges). Versatility simplifies the process of their use. Mostly universal putties are represented by polymeric compositions. The resulting surface layer is somewhat inferior in quality to the gradual finishing of the starting and finishing putty.
Release form
The readiness classification determines the state in which the filler material is located at the time of sale. It is subdivided into 2 groups: dry mix and ready solution.
Dry mix
This material is sold in bags of different weights. Consider its key features.
- For a qualitative result, proper mixing of such a solution is necessary, which will ensure the uniformity of the mass and the absence of various lumps in it, otherwise the surface will be far from the desired one.
- The shelf life of dry mixes is much longer than other analogues.This is important if you purchase material for finishing various rooms, in which you can work through a certain period of time.
- In financial terms, dry mixes are cheaper because they do not contain additional additives that maintain a suitable state of the finished solution.
- It is more expedient to apply dry mixes when an ideal surface is not necessary (for example, for the starting layer or when pasting the surface with thick wallpaper).
Ready solution
The finished mixture is mainly produced in buckets of various sizes (from 2 to 40 kilograms). This material has its own characteristics.
- It is simpler to use ready mix, there is no need for presence of mixing skills.
- The finishing layer is characterized by evenness and perfect smoothness, it is the best option for painting or various design solutions.
- The shelf life of such putty is strictly limited and varies from the presence of special additives.
- The price of ready-made solutions, regardless of the type of putty, will be higher in composition than a similar dry mix.
Composition
Depending on the substances that make up the putty, the finished solution exhibits certain properties characteristic of this type. Gradation of classes occurs on the main binder.
Gypsum
This putty is widely used for finishing plasterboard surfaces. The simplicity and ease of handling have provided her with great popularity among professionals and only those who are familiar with the finishing work of people. The main qualities of such mixtures include several characteristics:
- They are used as a starting and finishing layer;
- dry mixture is diluted with little effort, it gives a soft and pleasant texture;
- they stretch well on the surface;
- they are characterized by a short period of setting and hardening;
- these compositions do not shrink, there will be no cracks on the frozen layer;
- the resulting surface is smooth and even;
- they have a pleasant aesthetic appearance (the finishing layer can be used as a front wall finish);
- This is a great option for painting and designer finishes;
- such a filler is characterized by affordable cost;
- they are easy to sand;
- it is distinguished by high plasticity;
- it has no specific building odor;
- this material can be stored for a long time at a low temperature;
- it has high thermal insulation performance and refractory;
- these compounds are non-toxic, their microparticles trapped in the air do not cause allergies;
However, a high level of moisture absorption of such fillers makes it inappropriate to use this type of finishing material in rooms with high humidity. Fragility determines the vulnerability to mechanical stress and vibration of the finished coating.
Cement
The putty, which contains cement, is distinguished by its budgetary cost, which makes it in demand when performing a large amount of preparatory work. These materials have their own characteristics.
- Sand is used for mixing, which has strict requirements (for example, the fraction of particles must be 1.5-2.5 mm, otherwise the cracking of the finish is almost guaranteed).
- The mixture should be dissolved with water at room temperature (about 20 degrees C).
- The rate of hardening putty varies in the range of 5-24 hours (depending on temperature conditions).
- The layer shrinks, which determines the need to reapply the composition after some time (after complete drying of the first layer).
The frozen layer has a significant roughness.This composition is resistant to temperature fluctuations, it is frost-resistant, characterized by durability and moisture resistance. However, during operation, and even immediately on the surface, cracking is possible, despite full compliance with the technology. In addition, these varieties are difficult to grind.
When hardened, the standard composition acquires an unaesthetic color, although today there are compositions of white and super-white shades modified with tinted pigments.
Polymer
Acrylic or latex-based putty blends are distinguished by their beautiful appearance on the finished surface.
- They can be used for any stage of puttying, however, due to the high cost, they are more often used for finishing putty.
- They are realized in the form of a dry mix and ready solutions.
- They give a smooth and smooth surface, regardless of the defects of the working surface.
- It is a good base surface for coloring and designer finishes.
- They improve the sound insulation of the surface.
- They are biologically inert, the coating material eliminates the proliferation of microorganisms (fungus and mold).
High vapor permeability allows free to evaporate moisture, which is under the finishing layer, as a result of which the room does not dampen. Moisture resistance is inherent in them: such material can be applied in bathrooms and kitchens. In addition, it has no smell.
To choose a putty for unheated premises, you need to choose a moisture-resistant and elastic material.
How to putty?
The end result depends largely on the correctly chosen putty mixture. An important factor is compliance with the rules, as well as consistent finishing work. Before work is necessary to prepare the tools, including the area, trowel, level. When choosing a primer is to give preference to the composition with high penetrating power. Consider the key points of the process.
Surface preparation
The working surface is cleaned from small debris (dust, dirt). Apply a primer solution, which give time for drying before continuing the finish.
Preparation of the solution
Dry mixture is diluted, according to the instructions of the trademark. It is necessary to thoroughly knead the solution, after which it should stand for about half an hour.
Before you repair the irregularities, you need to stir it again.
Seam processing
Mass impose on a large spatula small, and then put along the entire joint carefully to putty filled the groove. Further, it is uniformly pulled over the entire plane.
Masking screws
The solution is applied crosswise: it is necessary to ensure that the hollow is completely filled without possible voids, then it is leveled.
Self-tapping screws should not be visible.
Fillet corners
The process is similar to putty self-tapping screws. First, the mixture is applied to all sides of the corner, after which the solution is carefully ground to fill the voids and evenly drawn out to create a single plane.
Finish stage
First, those areas that have not been affected are treated, they create a common putty sheet (it is better to close them up in small portions). Next, leveling is performed over the entire surface with a thorough level check.
Grinding after sealing
After a certain time, the finished coating is treated with sandpaper or float to smooth out the existing flows.
Useful recommendations
When filling the surface under the gluing of paper wallpaper, kneading the solution should be done very carefully.The working plane should be different smoothness and evenness: this kind of wallpaper tend to emphasize any shortcomings. If the preparation of the base is carried out for pasting heavy wallpaper, it is better to use cement-based putty.
When puttying is done under dyeing, the surface is leveled to perfection.
You can find out how to putty the plasterboard ceiling in the following video.