Alkyd varnishes: types and their characteristics
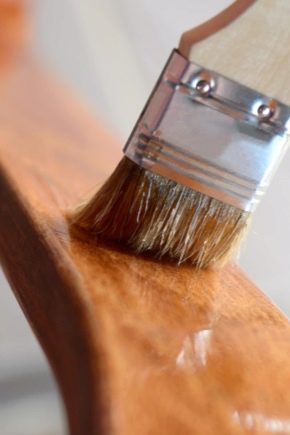
Treatment with protective compounds is necessary for almost every material and surface, especially for bases subjected to mechanical loads or factors that adversely affect their condition and appearance. This issue is relevant for wood and for metal. There are many different products on the market that are recommended for such materials, among which alkyd varnishes can be identified.
What it is?
This composition is a mixture of synthetic resins and solvents of natural origin. Varnish components provide it with a high level of adhesion and resistance to moisture.
Quality requirements for alkyd products set certain standards,to which the composition should correspond - first of all, the varnish should be colorless, and on the surface should form a glossy or matte protective layer. Some products may have a certain shade. The mixture allows you to increase the aesthetic appeal of the base, emphasizing the depth of color, which is important, for example, for the parquet floor.
As a result of use, the treated surface becomes more attractive. However, the choice of a product must be based on personal preferences and the scope of surface exploitation. Alkyd varnishes are somewhat different in their specificity and chemical content, depending on their use for indoor or outdoor use.
Alkyd mixtures are widely demanded in comparison with their counterparts. This is due to the operational properties of products, which are several times higher than the available indicators of oil formulations.
Specifications
The unchanged and main component of varnishes is an alkyd resin, which acts as a base. Among similar products, alkyd varnishes are out of competition in terms of resistance to temperature fluctuations.
Vibration loads do not affect the quality of the applied alkyd composition, in addition, the varnish does not have the adhesive quality that many representatives of paint and varnish products have. The tool is absorbed directly into the tree and does not penetrate into the genital slits in the log house. Such characteristics of products allow minimizing squeaks of floorboards when treating the floor with an alkyd mixture.
The first varnish on alkyd basis, which was produced in Russia, is the composition of the PF-231. The product is intended for use on all types of surfaces. It may be noted the external attractiveness of the base obtained after treatment with this composition - the film evenly and gently covers the working surface.
In addition to the positive characteristics of the composition has some disadvantages. The main disadvantage is the short operational life of the coating due to its minimum hardness. Due to this, after 2-3 years the surface of the wooden floor will have to be processed again. On other materials composition will serve many times longer.
PF 283 forms a glossy layer, remarkable for its decorative properties. In essence, this product is a mixture of alkyd resin, fatty acids and solvents of natural origin. In addition, there is a desiccant among the ingredients.Most often, such a lacquer is sold in a spray like an aerosol of 150 ml.
PF-170 includes a resin in combination with specific additives and aliphatic hydrocarbons. The composition can be used for wood, wood-containing materials, metal and ceramic bases. In addition, the bases treated with paints, enamels and primers, very often cover these very protective and decorative composition. Products are allowed for use indoors and outdoors. The lacquer is manufactured according to GOST, is resistant to chemical detergents and aggressive environmental factors, allows the surface to "breathe" and is very economical in terms of consumption.
Benefit and harm
The advantages of alkyd varnishes include the following characteristics:
- resistance to fluctuations in temperature and humidity;
- vibration resistance;
- lack of adhesive properties;
- high decorative qualities of the obtained coating;
- when using the brush, the composition is applied very quickly, because it has a thick consistency;
- after drying, a glossy or matte film is formed on the substrate;
- resistance to mechanical stress;
- the composition does not lose its properties upon contact with chemical compounds;
- prevents the formation of mold or mildew on the material.
According to consumer reviews, the following disadvantages of alkyd formulations are highlighted:
- For the complete polymerization of the mixture takes a lot of time, usually this period is about a day. To eliminate this disadvantage, most manufacturers began to include hardeners in the composition, which reduce the time required for the mixture to dry.
- Not until the end of the dried base, treated with alkyd varnish, has a sharp peculiar smell that is dangerous to human health. To eliminate the risk of vapor poisoning, allow the room to be well ventilated during the curing of the film.
- Excessive amount of alkyd mixture necessarily shrinks on the ground, so when working with products, you must follow the instructions.
Kinds
There are several types of alkyd varnishes.
Two pack
They consist of two components, as the second component acts as a desiccant. Before applying the mixture is required to combine into one composition in a ratio that indicates the manufacturer.After that you can start painting. Usually for durable and high-quality coating requires surface treatment in 2 or 3 layers.
An important feature of such compositions is the small shelf life of the finished mixture - the solution is suitable for work for 8 hours. According to its characteristics, the compositions differ by the highest rates. However, lacquer has a strong odor, as well as a low indicator of resistance to sunlight.
Alkyd urethane
It becomes popular due to the characteristics of the mixture in which alkyds react with polyurethane. The mixture will be improved due to a special component - toluylene diisocyanate, due to which the process of drying lacquer is carried out a little differently. First of all, the solvent evaporates, and after that the mixture already solidifies when exposed to oxygen. The drying time of the surface with this mechanism of drying is reduced, in addition, improved indicators of resistance to abrasion, temperature effects and high humidity.
This pattern causes an increase in the operational period of coverage, which is explained by the high demand for products, as well as its high cost.
However, due to the fact that half alkyd-urethane varnish consists of an organic solvent, its toxicity increases. Also, the product is unsafe in terms of fire, therefore, the operation of coatings requires the observance of additional safety measures. In addition, if the coating does not dry out completely, and the base is already in use, situations are inevitable in which the lacquer deforms to form serious defects. You can only remove them with a grinder.
Matte and glossy
Compositions differ only in what texture has a dried base after processing. The opaque composition forms a more practical surface, since there are less visible dirt and traces on it, there are also semi-mat mixtures. Gloss is best used in rooms with minimal lighting, as it perfectly reflects light. In terms of the set of components, both products do not differ at all, which is why the choice of the mixture will be based only on the consumer's taste preferences.
Yacht
Based on the name, the scope of use of the products becomes clear - the mixture is produced to cover wooden yachts,but in addition to the processing of ships, such a specialized composition can be used on grounds that are operated in wet microclimate conditions. However, you should pay attention that yacht varnish can be used only for outdoor work.
This limitation is explained by the chemical composition of the material - to increase its resistance to moisture during the manufacture of varnish, its main set of essential elements include toxins, for example, toluene.
For metal
In composition, it is a mixture of alkyds and polymers. Substances provide metallic bases shine and attractive appearance. The mixture has high resistance to chemically aggressive substances, high humidity, thermal effects on the surface, in addition, adhesion to various types of material makes it possible to exploit the varnish inside and outside the premises.
To properly perform work on the application of alkyd varnish, you need to perform a primer or puttying the surface. Also, before applying the base must be cleaned from dust and dirt and degrease.
To achieve a high quality result, it is better to use products from a single manufacturer. Alkyd compositions for parquet can be classified as follows:
- Water based blends. The advantage of solutions is the lack of odor and environmental friendliness of products. But such paints are high cost.
- Two-component varnishes.
- Single component formulations.
Based on the type of coating alkyd varnishes are divided into the following subtypes:
- glossy;
- matte;
- semi glossy;
- semi-matt.
To give the varnish color, some masters use colors that are selected based on the basis on which the composition is made and what kind of solvents are used. Thanks to this option, a tinted surface is formed on the material.
Application
It is possible to identify the main areas of use of alkyd varnishes:
- face parquet processing;
- parquet floor with heating;
- "Floating floors";
- parquet, for the manufacture of which were used very "capricious" wood species - their peculiarity is susceptibility to the influence of environmental factors;
- products for metal processing.
Consumption
The level of consumption of alkyd varnish depends on the type of composition used, as well as the professionalism of the master performing the treatment. Manufacturers and specialists agree that the composition should be applied in several layers. Usually requires 2-3 layers. It is very important to start applying the next layer only after the previous one has completely set. Based on this, it can be understood that the work will take at least 2 days.
The average consumption of alkyd mixtures is 50-70 g / m2. Some types of alkyd varnishes need to be diluted before application.
What to dilute?
White spirit is used as a solvent for alkyd compounds, which begins to evaporate as soon as the composition has been applied to the surface. Then there is a polymerization composition. It is caused by chemical reactions between the molecules of the resins and other components.
To remove the lacquer coating from the surface, use the remover. It is a special chemical agent that destroys the lacquer and lifts the film from the material. You can wash off the lacquer with powder means, a paste of different consistency, as well as cycling or by heat treatment.
How long does it dry?
Immediately after applying the alkyd varnish is similar to glue ,. After about 10 hours, some varnishes with special hardeners in the composition, already hardened. Usually it takes 24 hours to dry one coat.
It is worth paying attention that after drying, the thickness of the lacquer film may become less, in which case everything depends on how much of the solvent has evaporated. Its content in alkyd mixtures can be different, and based on this indicator, the level of toxicity of the composition increases or decreases.
For more on alkyd varnish, see below.