Aluminous Cement: Features and Applications
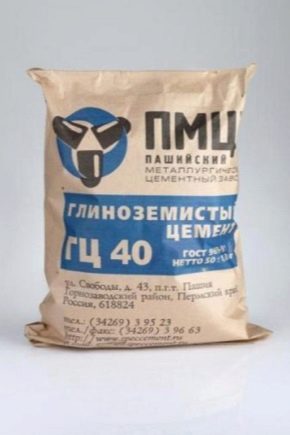
There are building materials, without which the construction of buildings or structures for various purposes and configuration can not be performed. Such products include cement on the market in a wide variety. Among the available list can be identified alumina cement, the popularity of which is due to a number of specific characteristics.
Manufacturing features
Raw materials such as cement, is a group of products, which consists of hydraulic substances based on aluminates and silicates, formed during the heat treatment of components.
A special place in the line of these goods is given to the construction mixture of a high-speed type, the main characteristic of which is the ability of the material to freeze not only in contact with air, but also in water.These products are called high alumina cement. In addition, there are other product names, such as aluminate cement.
The production of raw materials is carried out using a special technology, during which the basic components are additionally enriched with alumina. After that, the composition undergoes heat treatment in a blast furnace or electric arc factory furnaces, and then crushed to the required particle size. The chemical formula and technical characteristics of these products allow to use it for the preparation of heat-resistant concrete. The main distinctive feature of alumina cement from raw materials of other brands is fire resistance, which is several times higher than similar indicators of products of other companies, for example, Portland cement. According to experts, the composition of the mixture allows it to operate at temperature values reaching 1700C.
Alumina cement is often used as one of the components in various compositions, mixing with magnesite or chamotte, which allows the manufacture of hydraulically hardening fire-resistant solutions.
Cement production is carried out on the basis of bauxite and limestone in combination with a number of other substances that are responsible for certain characteristics of the composition. Modern production facilities use two methods of producing the composition according to GOST - sintering and melting. The choice of production method is based on the specificity of the composition of bauxite and the level of content in the elements of different inclusions, for example, iron oxide.
During the selection of the latter method of manufacture, very high demands are placed on the quality of bauxite. The process begins with the immersion of the composition in a water-cooled oven. Hot air, the supply of which occurs through the tuyeres, provides a procedure for melting the composition. At the end of processing, the raw material is cooled and crushed.
Much less often resorted to arc melting method, thanks to which the highest quality characteristics are inherent in the cement.
After production, further preparation of the composition is carried out, which includes the mixing of all ingredients. Then they are granulated or briquetted.
When used to release alumina cement blast furnaces As a result of production, high-alumina slag is formed, in which no iron is present, but there is a high content of silica. Such products have the disadvantage associated with the minimum strength of the composition at the beginning of its hardening. In domestic production, the method of obtaining a cement mixture by blast smelting has become very popular.
Sintering process - a method of manufacturing alumina cement in factory furnaces of the usual type with a slight heat. During the gradual cooling of the raw material, the genelite, which is part of it, crystallizes and acquires a glassy structure. The control of the heating level during such a production process is fundamental, since an insufficient heating level will contribute to the crystallization of calcium aluminates.
At the exit of the equipment, the composition is granulated. And the quality of the cement obtained in this way will allow products to stand out with the maximum strength values of the raw materials.
In some cases, apply method of electric melting composition. The advantage of this method is the purification of the composition from silicic acid.
When choosing the most suitable method of cement production, in addition to analyzing the chemical composition of bauxite, it is also worth considering the quality of coke and the cost of electricity. The combination of the above factors will help you choose a rational method of manufacturing raw materials.
Composition and properties
The main element of the cement is aluminate. During solidification, it becomes dicalcium hydroaluminate.
The composition can be classified into several types, based on the content of lime:
- low-lime mixture, where the indicator of the substance content is less than 40%;
- high lime product, where the presence of CaO is more than 40%.
Limestone or burnt lime act as a lime component. High lime production is notable for quick setting. Low-lime formulations have a longer solidification process.
In addition, the initial strength of such mixtures will be low.
Allocate the main chemical elements that are part of the alumina cement:
- iron oxide, whose content varies in the range of 5-15%;
- silicon oxide - up to 45%;
- aluminum oxide - from 20 to 50%;
- calcium oxide, the percentage of which can be from 30 to 40%.
The content of iron oxide is not regulated by GOST, but the amount of this element is of paramount importance for the production of alumina cement.
The mixture has a number of specific properties, among which the following should be noted:
- Products have high viscosity and strength. Such qualities are inherent in the mixture due to the presence in the substance of calcium aluminates. The technology of solidification of such a composition is no different from a similar process occurring with a PC. But a distinctive feature of the hardening of alumina cement is a significant heat release - in the first 24 hours about 70% of the heat is released, which is not always safe during construction. This is due to the fact that increasing the ambient temperature by more than 20% reduces the stability of the solution by 2 times.
- The alumina composition forms a dense stone, characterized by resistance to aggressive media. However, the action of alkali and lime is detrimental to it.
- The composition begins to harden after half an hour after pouring, this process is completed in about 12 hours.
- Alumina mixture is recommended for use at low temperatures, this is due to the level of heat.
- The mixture has high rates of resistance to aggressive gaseous substances and liquids. It retains its properties and structure in contact with chloride, carbonate and other waters due to the water resistance of the composition.
- In addition, the resistance of raw materials to high temperatures, including open fire, allows to characterize cement as a refractory material. Its qualities are only improved by the inclusion of ingredients such as magnesite and chrome ore.
- The most favorable temperature for hardening the composition is 25 ° C at the maximum humidity level.
- The use of alumina cement in construction increases the rate of adhesion of the solution to steel reinforcement, which, in turn, strengthens the monolith of the whole structure, positively affecting the durability of structures.
But, despite the impressive list of positive properties of cement, products have several disadvantages:
- The sensitivity of the raw materials to heat, exceeding 25C when the composition hardens. This may cause deformation of the structure.Therefore, it is not recommended to operate it in hot climatic conditions, or it is advised to shut it down with cold water.
- Products have a higher cost in comparison with the PC, due to which it is less in demand.
- Most of the alkali solutions will be able to destroy concrete and stone, in the composition of which there is alumina cement.
Structure and species
During production, two types of alumina cement can be produced. Taking into account the content of impurities, the mixture is classified as follows:
- standard composition;
- high alumina mixture.
It is possible to determine the brand of cement three days later after production. Since the product has a high cost, the composition is sold in small volumes.
The alumina composition is brown, yellow, green or black. Such differences in color are due to the content of iron in the mixture, and the shade also depends on the oxidation index of the ingredients in the composition.
In addition, there are products of white color, which incorporates the minimum amount of iron.
Products are packaged in special containers or bags.Product labeling is based on GOST. Based on this, There are three types of cement that differ in resistance to compression during loads:
- HZ-40;
- HZ-50;
- HZ-60.
Aluminous cement HZ-40 is characterized by an increase in strength within 72 hours from 22.5 to 40 MPa. Such a brand is most often purchased for construction purposes, its cost is more affordable compared to other brands, and the available properties will be quite enough to complete the tasks.
The next variety is characterized by indicators of strength, which increase to 50 MPa. Cement prefer to operate in the fuel and energy sector.
The latter type has the highest level of strength, reaching 60 MPa. Due to this feature, aluminous cement HZ-60 is widely used in metallurgy and defense industry.
Since the material has a rather viscous structure, it will take more time to mix it than for portland cement. The durability and homogeneity of the resulting concrete directly depends on how long the mixing will be.
For work, as a rule, the mixture is prepared in small volumes, since the cement does not contain components that slow down the process of solidification.As a result, the composition begins to set soon after preparation.
Among the manufacturers of the composition are the following companies known throughout the world: Ciment Fondu, Secar, Cimsa Icidac.
Application area
The main area of cement exploitation is still industrial construction. The demand for products in this area is explained by the presence of various kinds of objects where it is necessary to use raw materials that are resistant to high thermal effects, sometimes reaching up to 1300С. In addition to temperature, corrosive substances can affect the material.
In this case, the properties and stability of the alumina composition will be very useful.
It is necessary to highlight the main areas in which products are operated:
- With the help of the composition, the reconstruction and repair of the damaged bridge structures of different levels of complexity and configuration are carried out.
- The mixture is in great demand in cases when high-speed construction of structures is required with the acquisition of maximum stability of the building within 3 days.
- Alumina cement is used for construction purposes, namely where materials with sulphate resistance are needed.
- Fastening and fixing anchor bolts is carried out using an alumina composition.
- The manufacture of containers that will be operated in direct contact with aggressive substances, occurs with the inclusion of such a cement mixture.
- Production is used in work at arrangement of oil wells.
- Mix is applied as the accelerator to hardening of concrete.
- With the help of alumina cement repairs of ships.
- Repair work on the repair of leaks in the rock, which is accompanied by excessive water consumption, is performed by such a composition.
- Cement is also used to make refractory concrete.
- The mixture is used for the construction of reinforced concrete structures.
- Cement has found its use in the construction of underground and marine structures.
- The products are used as an additive in adhesive formulations, which are carried out in the field of building chemistry.
- The mixture acts as the main ingredient in the manufacture of waterproof and expanding compositions.
However, apart from operating in the industrial construction industry, alumina cement quite often used as construction products in the course of work related to private and home construction. Expansion of the field of application of the material is associated with the individual properties of the raw materials, but gypsum-alumina cement in everyday life is not used due to its high cost.
In order to get the maximum benefit from the operation of this product, it is necessary to take into account all the existing features of the raw materials that relate to its chemical composition.
It may be noted the following types of work in private construction, where it is appropriate to use alumina raw materials:
- preparatory work with window sills;
- construction of basements and basements in buildings;
- work related to the arrangement of screed for floors;
- reconstruction and repair of the ventilation system and chimneys in the house;
- construction of fire chambers, fireplaces and other types of heating devices, quite often used in private homes.
You can find out how to knead cement mortar properly by looking at the video below.