Subtelności wyboru cementu
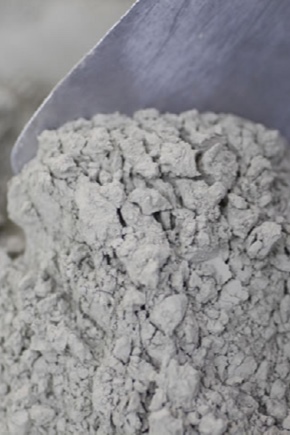
Ani jeden budynek nie może obejść się bez cementu i bez względu na rodzaj domu - cegłę lub drewno. Jedyna różnica jest ograniczona tylko do wymaganej ilości mieszanki. Ten materiał budowlany jest z powodzeniem stosowany od ponad wieku ze względu na jego wysoką jakość i doskonałe właściwości operacyjne.
Funkcje produkcyjne
Gdy tylko ludzie zaczęli budować domy, potrzebowali kompozycji, która mogłaby trzymać kamienie i inne materiały budowlane razem. Początkowo była to zwykła glina, ale takie mieszkania były krótkotrwałe, a sam budynek wyglądał całkiem nie do opisania.
Nieco później budowniczowie odkryli, że zaprawa wapienna ma również pewne właściwości wiążące - to odkrycie dokonali starożytni Grecy i Rzymianie, a ten zauważył, że jeśli do wapna dodano popiół wulkaniczny, układanie stało się naprawdę monolityczne.
Wapno było używane w Rosji, mieszając go z gliną i wodą. Na początku XIX wieku w wyniku eksperymentu powstała mieszanka budowlana, która w swoich parametrach zbliżona jest do nowoczesnych kompozycji.
Cement jest więc definicją materiału składającego się z gliny i składników wapiennych. Są one mieszane ze sobą i poddawane długotrwałej obróbce cieplnej, po czym uzyskana masa jest mielona na proszek.
Mieszanina ma szary odcień i podczas interakcji z wodą tworzy roztwór, który po wyschnięciu staje się twardy jak kamień. Jego wyjątkową cechą jest to masa twardnieje tylko w warunkach wysokiej wilgotnościi ten proces może wystąpić nawet pod wodą. To, przy okazji, główna różnica między cementem a wieloma innymi spoiwami.
Na przykład gips i wapno powietrzne nabierają siły tylko w powietrzu. Jako część betonu twardnieje nie tyle dlatego, że woda odparowuje, ale raczej w wyniku reakcji z proszkiem: w tym momencie uwalniane jest ciepło i tworzą się substancje stałe lub krystaliczne. Dlatego proces mieszania samej mieszaniny jest często nazywany migawką i wcale nie rozpuszczeniem.
Monolityczna masa powstaje w wyniku hydratacji cementu, betonu nie należy suszyć w palącym słońcu - po prostu „łzy”, pękają i bardzo szybko zaczynają się kruszyć.
Aby uniknąć takich nieprzyjemnych sytuacji i zaoszczędzić pieniądze, zaleca się zwilżanie roztworu betonu, aż do całkowitego wyschnięcia.
Zajmiemy się trochę więcej o cechach produkcji.
W pierwszym etapie uzyskuje się wapień, tufy kredy, margla i wapna są uważane za najlepsze, ale nie zaleca się stosowania różnych gipsów i dolomitów - wytrzymałość cementu na ich podstawie pozostawia wiele do życzenia. Następnie surowiec miesza się z gliną w stosunku 3: 1 i otrzymaną mieszaninę przesyła się do pieca obrotowego, ogrzanego do 1400-1500 stopni.
To właśnie ta temperatura zapewnia maksymalne spiekanie, w którym składniki gliny i wapienia topią się i rozpraszają między sobą.
Po 3-4 godzinach kompozycja opuszcza piec, w tym momencie składa się z wielu grudek o różnych rozmiarach - jest to klinkier cementowy, następnie kruszy się do cząstek o wielkości mniejszej niż 100 mikronów, na tym etapie do kompozycji wprowadza się 6% gips - jest to konieczne dla nie wchłaniał wilgoci z powietrza.
Oprócz gipsu dodaje się inne aktywne składniki, które poprawiają właściwości cementu i pozwalają na jego zastosowanie w różnych sektorach budowlanych: wszystkie dodatki dają pewne parametry cementu, na przykład hydrofobowe lub szybko twardniejące materiały budowlane, a beton jest produkowany w połączeniu z CBC.
Właściwości i specyfikacje
Rozważ podstawowe właściwości cementu.
Próba szlifowania
Ten parametr określa szybkość twardnienia zaprawy cementowej i wytrzymałość powstałego kamienia. Zależność tutaj jest odwrotna - im mniej szlifowania - tym szybszy proces krzepnięcia i silniejszy powstający monolit. W związku z tym ceny cementu drobnoziarnistego są wyższe.
Stopień rozdrobnienia określa się za pomocą wskaźnika powierzchni właściwej i składu ziaren, w tym celu materiał przesiewa się przez sito ultradrobne, którego rozmiary komórek nie osiągają nawet 8 mikronów, podczas gdy masę cementu należy łatwo przesiewać.
Z drugiej strony im mniejsze szlifowanie, tym więcej wody jest potrzebne do rozcieńczenia cementu. Dlatego wprowadzenie zarówno dużych, jak i małych cząstek w zakresie od 40 do 80 mikronów do struktury jest uważane za optymalne.
Aby uzyskać szybko utwardzalny rodzaj cementu, koniecznie trzeba dodać do 25% cząstek; bardzo dokładne szlifowanie - znacznie zwiększają jego wytrzymałość i zmniejszają ryzyko korozji.
Odporność na korozję
Podczas pracy roztwory wody i kwasu mają stały wpływ na kamień cementowy, co prowadzi do korozji konstrukcji żelbetowych. Aby tego uniknąć, do kompozycji wprowadza się specjalne materiały hydroaktywne, które znacznie spowalniają, jeśli nie całkowicie łagodzą aktywność soli chemicznych, a także przyczyniają się do hydroizolacji wyrobów betonowych.
Z reguły stosowane są dodatki oparte na polimerach, które znacznie zmniejszają porowatość substancji i zwiększają jej odporność na niekorzystne czynniki zewnętrzne.
Dzięki wprowadzeniu takich komponentów cement staje się naprawdę trwałym i niezawodnym materiałem.
Mrozoodporność
Aby wykonać beton wysokiej jakości, konieczne jest stosowanie tylko wysokiej jakości cementu, ponieważ podczas przechowywania każda kompozycja wchłania wilgoć z powietrza w mikro dawkach. W niskich temperaturach zamarza i zwiększa swoją objętość o 7–10%, a przy powtarzającym się powtarzaniu powoduje poważne uszkodzenia betonu w przyszłości.
W warunkach stale rosnących cen materiałów budowlanych właściwość utrzymania jej wydajności pod wpływem niskich temperatur nabiera szczególnej wartości.
Nowoczesne kompozycje cementowe są tworzone w taki sposób, aby wielokrotnie wytrzymywać cykl zamrażania i rozmrażania.
Aby uzyskać dobrą mrozoodporność, abietat sodowy, smołę drzewną i inne składniki wprowadza się do czystego cementu., które powodują odporność kompozycji na temperaturę i zwiększają trwałość betonu jako całości.
Do struktury wprowadzane są również specjalne dodatki napowietrzające, dzięki czemu struktura jest wzbogacona pęcherzykami powietrza, skutecznie rozwiązują problemy rozszerzania się płynu podczas krzepnięcia.
Zapotrzebowanie na wodę
Gęstość fizyczna ziaren cementu jest kilkakrotnie wyższa niż gęstość wody, dlatego gdy jest zbyt nasycona, siły kapilarne zatrzymują tylko część wilgoci wewnątrz, a reszta jest doprowadzana na powierzchnię mieszaniny. Powoduje to sedymentację cząstek, co z kolei wpływa na zmniejszenie wytrzymałości całej konstrukcji betonowej i przyczynia się do jej szybkiego zniszczenia.
Zdolność cementu do zapotrzebowania na wodę zależy od ilości płynu potrzebnego do przygotowania roztworu roboczego. Jest mierzona w procentach, na przykład w cemencie portlandzkim, ta liczba wynosi 22-28%. Jeśli zapotrzebowanie na wodę jest niskie, to z takiego materiału uzyskuje się bardziej trwały i mrozoodporny beton.jeśli ten wskaźnik jest zawyżony, wówczas materiały uzyskane z kompozycji będą się różnić pod względem specjalnej porowatości i nie będą trwać długo.
Ustawianie prędkości
Idealnie rozwiązanie powinno być ustawione i nie powinno być szybkie ani powolne. Ponadto na czas wpływają dodatki, a także objętość cieczy i temperatura powietrza. Przyjęta norma wskazuje, że zamrażanie powinno rozpocząć się 35–40 minut po wytworzeniu zawiesiny cementowej.
W celu całkowitego zestalenia trwa około 10 godzin.
Parametry wytrzymałościowe
Wskaźnik wytrzymałości cementu oblicza się metodą kompresji próbki, którą przeprowadza się przez 28 dni. Podczas testowania cementów różnych marek wytrzymałość na ściskanie jest również inna. Nowoczesny przemysł produkuje cementy, dla których wskaźnik ten wynosi 300, 600, a także 700 i 1000.
Wielu konsumentów uważa, że główną cechą cementu jest siła, na którą należy najpierw zwrócić uwagę. To nie jest tak - wszystkie parametry kompozycji mają tę samą wartość i równie wpływają na wytrzymałość i trwałość konstrukcji betonowych.
Gatunki
Nie ma oficjalnej klasyfikacji cementów. W najbardziej ogólnym znaczeniu można rozróżnić kilka grup kompozycji, których kryteria opierają się na różnych parametrach.
Tak więc, w zależności od docelowej kompozycji emitują konstrukcję ogólną i specjalne kompozycje. Jeśli podstawą jest skład, wówczas możliwe jest wyznaczenie wariantów z min. dodatki i czysty cement.
Jeśli klasyfikujemy cement w zależności od szybkości utwardzania, najczęściej stosuje się następujące opcje:
- mieszanki szybkowiążące - tych, których stopa zamrożenia jest mniejsza niż 45 minut;
- normalne ustawienie - utwardzić w ciągu 45–120 minut;
- wolne utwardzanie - zamrozić przez 2 godziny.
Emitują również napięte, ognioodporne, samorozprężalne cementy i wiele innych.
Zatrzymajmy się na najpopularniejszych typach:
- Biały cement - Jest to materiał produkowany z klinkieru o niskiej zawartości żelaza, który ulega bieleniu. Jest to materiał o wyjątkowych właściwościach, może być stosowany nie tylko do klejenia powierzchni, ale także do produkcji elementów rzeźbiarskich i kolumn, a także do okładania elewacji budynku. Ze względu na kolor, użycie białego cementu pozwala poprawić estetyczny komponent powierzchni. Dodając pewne pigmenty, można uzyskać kolorowy cement.
- Wodoodporny rozszerzalny cement Jest substancją o wysokim współczynniku wiązania i twardnienia. Jest wytwarzany w procesie jednoczesnego mielenia cementu, gipsu i wodorowęglanu wapnia. Taki cement zaczyna się wiązać już po 4 minutach od momentu wymieszania, w końcu schnie w ciągu 10 minut.
Ten materiał jest szeroko stosowany do uszczelniania szwów i ich uszczelniania.
- Wodoodporny cement niekurczliwy - podstawowy skład składników takiego cementu jest taki sam, jednak technologia przetwarzania i produkcji sprawia, że szybkość utwardzania jest jeszcze większa - całkowite wysuszenie kompozycji zajmuje nie więcej niż 5 minut. Ta kompozycja jest używana do tworzenia powłoki hydroizolacyjnej dla produktów betonowych.
- Szybko twardniejący cement portlandzki - jest to cement raczej drobno zmiażdżony, dzięki czemu jest bardziej intensywny niż standardowy cement portlandzki. Materiał nabiera szczególnej wytrzymałości w początkowej fazie krzepnięcia - po 1-3 dniach. Najczęściej jest używany podczas przeprowadzania napraw.
- Plastyfikowany cement portlandzki - skład, w procesie produkcji którego do mielenia klinkieru wprowadza się 0,25% zacieru na bazie siarczynoalkoholu, dzięki czemu znacznie wzrasta mrozoodporność mieszaniny i jej plastyfikacja.
- Cement hydrofobowy - wykonane przez wspólne mielenie klinkieru cementu portlandzkiego i gipsu, a także wprowadzenie axilolu lub innych dodatków hydrofobowych. Absorpcja wody przez taki cement jest niska, ponieważ może być przechowywana przez długi czas nawet w warunkach wysokiej wilgotności, co nie pogarsza jego właściwości fizycznych i technicznych. Ta mieszanina nie tworzy grudek, a beton na jego podstawie nie pęka z czasem i nie rozwarstwia się.
- Cement glinowy - Spoiwo hydrauliczne wykonane z surowców bogatych w tlenek glinu, zwykle wapienia lub boksytu. Materiał twardnieje w niskich temperaturach, więc jest powszechnie używany do prac naprawczych w sezonie zimowym.
- Cement magnezowy - otrzymuje się z surowców bogatych w tlenek magnezu. Znalazł zastosowanie w układaniu podłóg magnezowych.
- Cement portlandzki - otrzymuje się go przez mielenie klinkieru cementu portlandzkiego z gipsem i specjalnymi dodatkami, technologia spalania jest skonstruowana w taki sposób, że zawartość krzemianów wapnia jest wysoka w otrzymanym produkcie.
- Pucolanowy cement portlandzki - te materiały budowlane zawierają w swojej strukturze składniki pochodzenia wulkanicznego. Kompozycja ta szybko twardnieje zarówno na otwartym powietrzu, jak i w wodzie, podczas gdy mieszaniny na bazie takiego cementu nie dają żadnych wykwitów i są wysoce higroskopijne. Z reguły taki materiał jest używany przy wyposażaniu basenów.
- Cementoodporny cement wykorzystuje się do produkcji piasku kwarcowego i fluorku sodu, kompozycja ta jest odporna na większość kwasów mineralnych i organicznych, nie zmienia swoich właściwości w wodzie. Jednak reakcja z alkaliami zaczyna się załamywać.
Znakowanie
Wszystkie rodzaje cementu mają specjalne oznaczenia, które odzwierciedlają ich zakres zastosowania. Znakowanie składa się z liter i cyfr.
- BOC - Cement portlandzki.
- SS - cement odporny na siarczany.
- SHPC - Żużel cementu portlandzkiego.
- Gf - kompozycja hydrofobowa.
- BC - biały.
- Łódź podwodna - uplastyczniony cement.
- VRTS - wodoodporny.
Stopień wytrzymałości spoiwa jest oznaczony literą „M” i liczbą, na przykład M500 - oznacza to, że taki materiał może wytrzymać obciążenie do 50 kg / m2. Zdarza się, że ta cecha jest po prostu oznaczona liczbą - 22,5, 42,5 lub 52,5 - to nie jest marka, ale klasa. Pokazuje, że materiał może wytrzymać ciśnienie, na przykład 22,5 MPa.
Litery A i B wskazują liczbę dodatkowych komponentów: A oznacza, że ich procent wynosi 6–20%, a B - od 21 do 35%.
Zakres zastosowania
Cement jest najpopularniejszym i najpopularniejszym materiałem budowlanym, jego zakres zastosowania jest praktycznie nieograniczony. Jest on stosowany w budownictwie na wszystkich etapach: budowa fundamentów, układanie piwnicy, układanie ścian, układanie dachów, instalowanie armatury wodociągowej, układanie cementów w konstrukcjach podłogowych. Używając materiału, produkowane są bloki.
Główną funkcją cementu jest wiązanie elementów konstrukcyjnych budowanych budynków, a także wyrównanie powierzchni wszystkich typów. Żaden cement nie może obejść się bez cementu, nawet najmniejszej naprawy.
Na szczególną uwagę zasługuje zakres stosowania specjalistycznych cementów:
- PC500 - jest szeroko stosowany do produkcji konstrukcji żelbetowych i wyrobów betonowych, a także w budownictwie przemysłowym i cywilnym - w tych branżach powstają maksymalne wymagania dotyczące higroskopijności, mrozoodporności i trwałości mieszanek budowlanych. Ponadto cement tej kategorii jest często używany podczas prac awaryjnych i naprawczych - wynika to z wyjątkowo wysokiej wytrzymałości początkowej betonu.
- PC500D20 - ten związek jest szeroko stosowany w budownictwie wszelkiego rodzaju: mieszkaniowym, przemysłowym i rolniczym.Materiał jest używany do produkcji prefabrykowanych konstrukcji betonowych, różnych elementów belek i sufitów.
Ponadto cement ten jest podstawowym materiałem do uprawy betonowych rozwiązań, które są stosowane podczas tynkowania i prac murarskich.
Głównymi zaletami tego cementu są mrozoodporność i wysoka odporność na korozję, dlatego marka cieszy się większą cyrkulacją niż zwykły cement portlandzki.
- PC400D0 - tego rodzaju kompozycje budowlane są wymagane do wytwarzania konstrukcji wykonanych ze zbrojonego betonu, a także do instalacji możliwych struktur podwodnych i powierzchniowych, które są narażone na znaczące działanie soli fizjologicznej i słodkiej wody.
- PC400D20 - niezbędne do produkcji prefabrykowanych konstrukcji żelbetowych, belek, paneli ściennych i innych materiałów niezbędnych do budowy.
Cement służy do układania ścieżek wiejskich, izolowania piwnic i tworzenia monolitycznej piwnicy oraz wielu innych rodzajów prac, zakres jej zastosowania jest szeroki.
Jednak każdy z nich wymaga pewnych gatunków i rodzajów cementu, dlatego konieczne jest wcześniejsze wyjaśnienie wszystkich wymagań dotyczących użytych materiałów.
Okres trwałości
Trwałość każdego cementu wynosi kilka miesięcy. Jeśli zastosujesz się do pewnych zasad, możesz użyć zaległej kompozycji. Należy jednak pamiętać, że jest to dopuszczalne tylko w przypadku układania struktur niekrytycznych. Wielu budowniczych z niewielkim doświadczeniem zawodowym kupuje cement luzem na przyszłość, ale nie jest to właściwe podejście.
Zgodnie z GOST 10178-85, każdy rodzaj cementu ma określony okres przydatności do spożycia, należy szczególnie podkreślić, że okres ten jest dopuszczalny tylko w przypadku tworzenia określonych warunków przechowywania materiału:
- do preparatów szybko twardniejących, pakowanych w worki lub pojemniki plastikowe - 45 dni;
- do cementu ogólnego przeznaczenia, pakowanie w miękkie pojemniki - 60 dni;
- do cementu szybkowiążącego luzem - 45 dni;
- do cementu luzem - 60 dni.
Pomimo dość krótkiego okresu przechowywania cementu zgodnie z GOST, w praktyce możliwe jest wydłużenie okresu trwałości znaków M200, M500, M600, M700 i M400 na sześć miesięcy lub nawet rok. Jest to możliwe w wielu warunkach, a mianowicie cement jest pakowany w całościowe miękkie opakowanie i umieszczany w magazynie w suchym pomieszczeniu.
Pakowane materiały należy układać na drewnianych stosach lub paletach z tworzywa sztucznego, zachowując odległość od palet do poziomu podłogi co najmniej 10 cm, a następnie opakowania z cementem są ostrożnie pokrywane folią plastikową, a jeszcze lepiej każde opakowanie musi być zapakowane w plastikową torbę.
Jeśli spełnione są wszystkie warunki, okres przechowywania cementu można zwiększyć do kilku miesięcy. Aby lepiej zrozumieć konsekwencje niewłaściwego przechowywania, zastanówmy się bardziej szczegółowo, co dzieje się z cementem w warunkach dużej wilgotności i dwutlenku węgla zawartego w atmosferze.
Jak już wspomniano, wszelkie zmineralizowane wióry i skład cementu są higroskopijnymi substancjami, które dobrze pochłaniają wilgoć, a gdy wilgoć jest pochłaniana z powietrza, rozpoczyna się proces hydratacji, w którym cement reaguje z wodą i w wyniku tego tworzy się krystaliczny hydrat. Takie materiały nie nadają się do użytku..
W produkcji cementu wszystkie podstawowe składniki klinkieru poddaje się obróbce cieplnej w temperaturach do 1000 stopni i powyżej, zachodzi dekarbonizacja, to znaczy materiał wyjściowy jest dzielony na wapno, dwutlenek węgla i tlenek wapnia. Ten ostatni z kolei przechodzi szereg metamorfoz, w wyniku których powstaje silny cement, a dwutlenek węgla trafia do powietrza.
Podczas długotrwałego przechowywania zachodzi reakcja odwrotna - dwutlenek węgla jest absorbowany przez główne składniki cementu, w wyniku czego parametry wytrzymałości i wydajności kompozycji są zmniejszone.
Producenci
Trudno powiedzieć, które marki tworzą najwyższej jakości mieszanki cementowe. Rynek budowlany jest wypełniony propozycjami różnych producentów krajowych i zagranicznych, z których każdy sprzedaje kompozycje o różnych oznaczeniach i parametrach.
Kilka lat temu rozważano absolutnego lidera na rynku cementu Koncern Holderbank (Szwajcaria) obejmuje przedsiębiorstwa w 70 krajach świata, a ilość wyprodukowanego cementu przekracza 100 milionów ton - liczba ta odpowiada połowie światowej produkcji rocznie. Holderbank produkuje najwyższej jakości cement na zaawansowanych technologicznie urządzeniach. Wszystkie sprzedawane produkty spełniają międzynarodowe normy EN 197-1.
Jednak całkiem niedawno lider się zmienił. Palma została schwytana przez francuską fabrykę Grupa Lafargektóry ma swoje zakłady w Europie, Azji i Ameryce i zamyka trzy najlepsze Cemex (Meksyk).
Wśród rosyjskich przedsiębiorstw produkty trzech marek cieszą się największym popytem:
- Grupa Eurocement - jest liderem krajowego segmentu, którego moce produkcyjne obejmują zakłady w 16 regionach naszego kraju. Użytkownicy zauważają, że cement tej marki jest najlepszy pod względem ceny.
- Nowość - To drugi co do wielkości krajowy producent mieszanek cementowych pod względem sprzedaży, jego produkty sprzedawane są w największych hipermarketach budowlanych w różnych miastach Rosji, pakując po 50 kg.
- Cement syberyjski - inny znany producent, który ustanowił pełny cykl produkcji cementu, jest jednym z trzech wiodących rosyjskich producentów, którzy wprowadzają na rynek tylko najwyższej jakości i praktyczny materiał.
Wskazówki
W ostatnich latach budowa znacznie wzrosła, a zapotrzebowanie na cement wzrosło. Doprowadziło to do powstania dużej liczby pozbawionych skrupułów producentów, którzy produkują cement z dodatkiem dodatków, które pogarszają jego właściwości operacyjne.
Aby się nie mylić, powinieneś dokładnie wiedzieć, jak dobry powinien wyglądać cement i na co zwrócić uwagę przy zakupie.
Specjaliści podają kilka aktualnych zaleceń:
- Z reguły cement sprzedawany jest w workach lub luzem. Korzystne jest kupowanie mieszanki w opakowaniu, ponieważ była ona chroniona przed niekorzystnym wpływem środowiska zewnętrznego na etapie przechowywania, a zatem zachowała swoje cechy konsumenckie.
- Na opakowaniu, zgodnie z wymogami prawa, obowiązkowe jest umieszczenie informacji o producencie, dacie wydania, GOST. Pod luźnym cementem można ukryć dowolną kompozycję.
- Jeśli cement jest kupowany w dużych ilościach, to każde opakowanie powinno być sprawdzone pod względem daty wydania, ponieważ w całkowitej objętości pozbawieni skrupułów sprzedawcy mogą mieszać nieświeży cement, a jak już wspomniano, aktywność kompozycji w ciągu sześciu miesięcy po uwolnieniu może się kilkakrotnie zmniejszyć.
- Świeżość cementu można sprawdzić niezależnie - w tym celu wystarczy uderzyć torbę dłonią, jeśli cement jest świeży, wtedy doznania nie przypominają uderzenia w kamień. Nawiasem mówiąc, cement w rogach opakowania jest przede wszystkim hartowany, więc zdecydowanie należy sprawdzić te obszary.
- Jeśli to możliwe, upewnij się, że cement jest przechowywany w suchym miejscu o dobrej wentylacji.
- Eksperci zalecają przeprowadzenie „eksperymentalnego” testu cementu, w tym celu należy pobrać wodę z wodorowęglanem sodu (na przykład zwykły Borjomi), uwolnić z niej cały gaz i zagnieść ciasto cementowe, z którego formuje się małe placki, tak aby grubość w środku wynosiła około 5 cm, a na brzegach - 1 cm. Wysokiej jakości cement powinien zacząć twardnieć nie później niż 10 minut, a jego pogrubiona część powinna się nagrzać w tym czasie.
Jeśli ani jedno, ani drugie nie wydarzyło się w ciągu pół godziny, odmów zakupu tej kompozycji.
W następnym filmie można obejrzeć proces produkcji cementu.